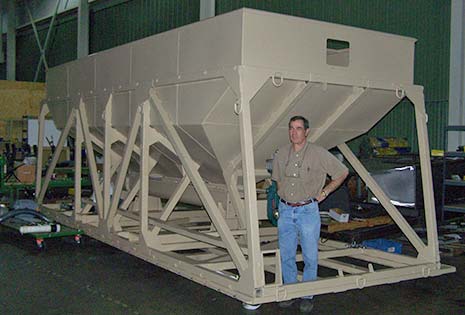
Southeastern Tool and Die offers both wet paint and powder coating. We have both a conveyor and a batch oven and can provide multiple color changes. We currently use Valspar, Sherwin Williams, and Akzo Nobel powder paint.
We are certified for military CARC (Chemical Agent Resistant Coating) wet, with or without a powder coat primer. We have Green, Tan, and Black CARC for all of our military customers. We utilize gas heat lamps for force curing of the CARC and wet coating for shorter curing times.
We Offer Four Types of Part Finishing
- Wet Spray Paint
- Powder Coating
- Plating
- for Military Customers, CARC paint
1. Wet Paint
Wet paint is a painting technique where a device sprays a coating (paint, ink, varnish, etc.) through the air onto a surface. This process requires extra care in the prep of the parts being painted. A ‘TAC” cloth is used to wipe the parts down to remove any trash or deposits left behind after washing the parts. The parts require a flash time to start the curing process and can take up to a couple of hours before dry enough to touch. Handling take more time 5 hours depending on the ambient temperature of the surrounding room.
2. Powder Coating
The invention of powder coating and the powder coating oven emerged as a response to the many issues that existed in the liquid finishing industry. The main issues were that the finishes did not last long enough, products contained a released volatile organic compounds when resins were being applied and the high costs associated with maintaining the proper safety equipment and pollution control units that were requires for applying traditional liquid finishes. In the 1940’s, the European finishing and coating industries were under tremendous pressure to find a more environmentally friendly way to process and dry coatings. The current method of coating was flame spraying, which utilizes combustible gasses to create the energy necessary to melt the coating material.
Why Powder Coat? Learn More ...
It was in the late 1940’s that Dr. Erwin Gemmer developed a way to fluidize the bed application for thermoplastic resins on metal as a more efficient alternative to flame spraying.
Powder Coating ProcessThe new powder coating method could be applied to new or used parts after they have been degreased and chemically cleaned to provide a proper surface. The coated part is then placed in a powder coating oven for 2-4 hours to complete the process.
Over the next 40 years, major improvements in coating and application processes and the efficiency of the powder coating oven brought the industry huge amounts of growth. By the 1980’s, the process and the powder coating oven had gained enormous popularity as breakthrough advances in resins and powder coating oven procedures had decreased waste, increased efficiency and lowered processing costs.
Today this coating can be applied and dried in a powder coating oven in as little as an hour. A standard powder coating oven on the market today can dry a coating resin in 15 minutes. These technological improvements continue to be driven by the automotive, aerospace, appliance and general industrial markets.
3. Plating
Metal plating provides many benefits to products made from metal and other materials. Plating is a manufacturing process in which a thin layer of metal coats a substrate. This can be achieved through electroplating, which requires an electric current, or through electroless plating, which is in autocatalytic chemical process. In either case, the technique results in one or several of the following benefits:
- Improved corrosion resistance
- Decorative appeal
- Increased solderability
- Enhanced strength
- Reduced friction
- Altered conductivity
- Enhanced paint adhesion
- Increased magnetism
4. CARC Painting
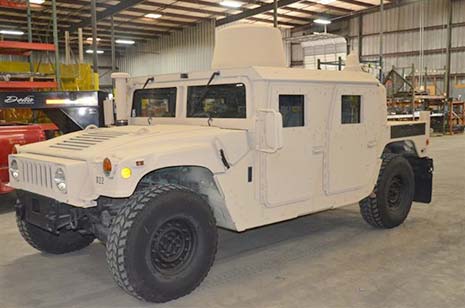
CARC (Chemical Agent Resistant Coating) is a paint commonly applied to military vehicles and equipment to provide protection against chemical and biological weapons. We offer Green, Tan, and Black CARC coatings.
The surface of the paint is engineered to be easily decontaminated after exposure to chemical warfare and biological warfare agents. The paint is also resistant to damage and removal by decontaminating solutions. Two-component systems (e.g. epoxy or polyester-based) are often employed. This coating is described in MIL-DTL-53072E.
The photos demonstrate our painting capabilities and processes.