Why Powder Coating?
Powder coating is an investment in your product and your company’s future.
- When you combine the robust reputation of powder coating with the increased pressure from environmental regulatory agencies, powder stands head and shoulders above other finishing technologies.
- Powder coating has gained a reputation for corrosive resistance and durability due to powders superior edge coverage, thick film build, and lack of primer requirement
- Powders are free from solvent and will not leave any traces of residual solvents in the coating film. Powder also has good resistance to hydrolysis, and low oxygen and moisture transmission.
What is Powder Coating?
Simply stated, it is a dry form of paint. Powder coating is based on polymer resin systems, combined with curatives, pigments, leveling agents, flow modifiers, and other additives. These ingredients are melt mixed, cooled, and ground into a uniform powder similar to baking flour. The product is packaged in plastic bags inside cardboard cartons.
A process called ESD (Electrostatic Spray Deposition) is typically used to achieve the application of the powder coating to a metal substrate. This application method uses a spray gun, which applies an electrostatic charge to the powder particles, which are then attracted to the grounded metal part.
After application of the powder coatings, the parts enter a curing oven where, with the addition of heat, the coating chemically reacts to produce long molecular chains resulting in high cross-link density. These molecular chains are very resistant to breakdown.
More Advantages of Powder Coating
- Ready for Use: They do not have to be mixed with other ingredients such as solvents or catalysts
- Coating Utilization: Coating losses with solvent-based paints are typically 15 – 25% of the applied coating. Overspray is instant wasted material. With powder, overspray materials can be re-used.
- Reduced Processing Times:There are no solvent flash-off times with powder and parts are ready to be handles after exiting the oven and cooling down is complete.
- Minimal Operator Training: Operators typically require much less training
- Maintenance: Powder coating systems provide lower expenses for maintenance and clean up.
In summary, powder coating is the best technology available to replace liquid painting processes. The combined considerations of cost, environmentally friendly, worker safety, and ease of use have made Powder Coatings the bright future in the finishing industry.
Finish Testing Explained
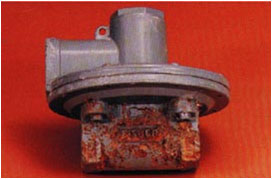
The standard method of testing the coating finish on parts is by “Salt Spray Testing”, a standardized test method used to check corrosion resistance of coated samples.
Since coatings can provide a high corrosion resistance through the intended life of the part in use, it is necessary to check corrosion resistance by other means. Salt spray test is an accelerated corrosion test that produces a corrosive attack to the coated samples in order to predict its suitability in use as a protective finish. The appearance of corrosion products (oxides) is evaluated after a period of time.
Test duration depends of the corrosion resistance of the coating; the more corrosion resistant the coating is, the longer the period in testing without showing signs of corrosion.
This part was powder coat painted and subjected to 500 hrs of salt spray testing.There is no specific correlation between the duration in salt spray test and the expected life of a coating, since corrosion is a very complicated process and can be influenced by many external factors. Nevertheless, salt spray test is widely used in the industrial sector for the evaluation of corrosion resistance of finished surfaces or parts.
So, Why Powder Coat?
- No solvent to mix and use
- Less waste from overspray and in correct mixtures
- Reduced Process Times for large jobs
- Minimal training needs
- Easy corrections of mistakes
- Low mainteance
- Easy re-use of any wasted product